THE PRINCIPLE
Well-designed – OMS hypoid bevel gear technology.
Well-designed – OMS hypoid bevel gear technology.
A drive principle that delivers what it promises – maximum efficiency with minimum backlash and smooth-running performance. OMS hypoid bevel gears have highly durable, arched teeth, similar to the axle drive in an automobile. Tooth geometry is key to ensuring smooth running and eliminating backlash. Developed in accordance with the GLEASON process, the geometry is implemented in high-performing gear technology thanks to highly optimized calculation, manufacturing, grinding, and testing processes. The interlocking tooth flanks unroll and glide to the side to form a perfect, hydrodynamic lubrication film and ensure practically wear-free operation with an efficiency of approx. = 96%. Proprietary SYNTEC TM gearing facilitates high gear reductions with a bevel gear stage without subsequent spur gear stage, for ultra compact drives. OMS hypoid bevel gear technology: an economical principal for powerful drives.
Advantages
Uncompromising quality – economical, convenient, and reliable.
Whether installed in an escalator or elevator drive – OMS hypoid gears quickly pay for themselves. From low space requirements to minimal maintenance work to the option for energy recovery, take advantage of all potential savings for economical operation.
Economical and quiet: thanks to its remarkably smooth-running performance and low noise emissions, guests using your system will enjoy outstanding comfort. Our systems offer all of this at a level of quality you can count on: OMS hypoid gears prove themselves everyday in over a hundred thousand escalators and elevators – under even the harshest conditions.
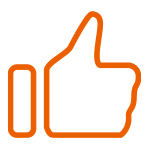
PROVEN
COMPACT
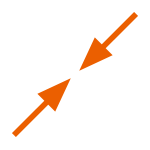
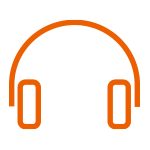
QUIET
LOW-MAINTENANCE
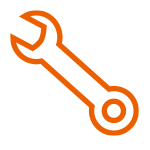
THE CONCEPT
Intelligent solutions at reasonable prices.
The modular principle makes it possible. OMS Drive technology offers complete drive solutions from a single source with components specifically tailored to work together. Thanks to the modular system, drives from the OMS Hypodrive series fulfill almost any usage or requirements profile. Regulated drives, for instance, with particularly low backlash are use in elevators that continuously change their direction of rotation. Drives for service escalators are designed for particularly long service lives of up to 140,000h. To optimally adapt OMS Hypodrive drives to elevator and escalator architectures, experienced designers from OMS Drive technology cooperate closely with system manufacturing specialists. This collaboration ensures the best possible drive configuration, a key requirement for guaranteeing the long-term, safe function of the overall system.
THE COMPONENTS
OMS Hypodrive – Drives made to order.
Dimensioned and designed to meet your individual profile of usage and requirements, experienced employees at OMS Drive technology manufacture your OMS Hypodrive drive to be unique.
We set the highest standards, not only for the quality of the individual components we use, but also for the reliability of the overall drive concept: from development to series production, OMS Drive technology conducts product tests throughout the entire process as a standard feature.
Transmission
Electric motors
Braking systems
Brake venting systems & emergency operating devices
Sensor safety systems
Frequency converter